Carbon neutrality through the power of plants?! Aisin develops the world's first bio-briquette charcoal for casting using coconut shells as raw materials
Nov.15, 2023
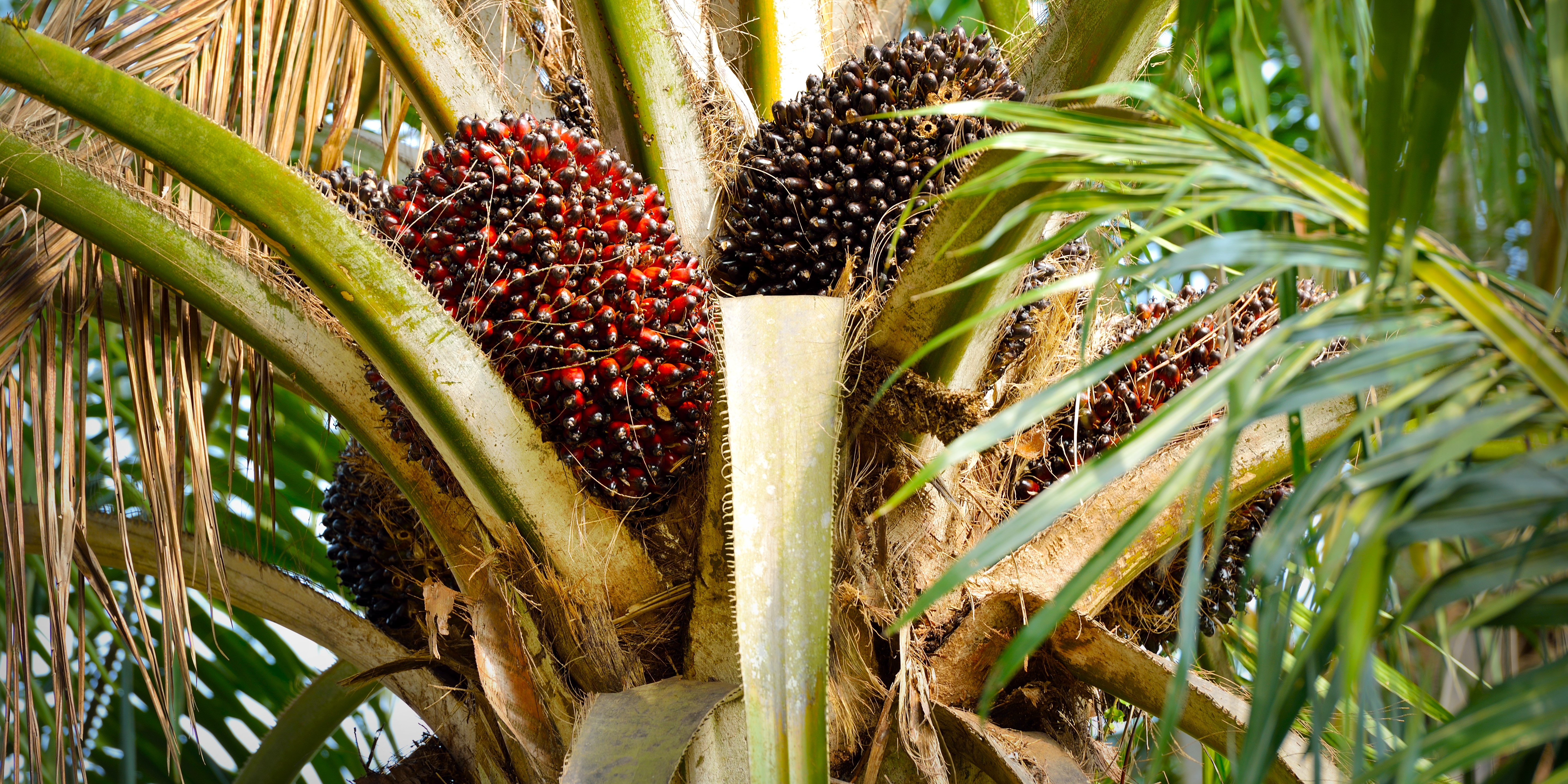
In our rapidly changing environment, global warming countermeasures have become a priority worldwide with special attention to developing biofuels that use plant-based biological resources.
Aisin Takaoka (Toyota City, Aichi Prefecture), a member of the AISIN Group that manufactures cast iron parts for automobiles, has developed the world’s first bio-briquette charcoal made from coconut shells as an alternative to coal-based fuel used in cast iron melting furnaces. It is our goal to reach a 100% replacement rate by 2030 and commercialize next-generation bioenergy that leverages the potential of plants. Through technological innovation in the field of cast iron, in which large amounts of CO2 are emitted, we will make significant progress toward our AISIN Group goal of achieving carbon neutrality (CN) by 2050.
Large amounts of CO2 emitted during the cast iron melting process
“Cast iron” is a general term for alloys that contain a large amount of carbon in iron. Adding carbon to iron makes it harder and more resistant to wear. A casting is made by pouring molten cast iron into a mold made of hardened sand and solidifying and cooling it. Castings are widely used in cast iron parts that are manufactured by Aisin Takaoka for the brakes and drive units of vehicles, as well as in familiar items such as household pots and manholes.
In the casting manufacturing process, coal-based coke is used as fuel to melt the iron source at a high temperature of about 1,500 degrees, resulting in a large amount of CO2 emissions. CO2 emissions at Aisin Takaoka in fiscal year 2022 were around 210,000 tons, and approximately 60% of these emissions came from the melting process. Accordingly, technological innovation in the melting process is essential to achieving CN.
During the melting process, the iron source and coke are alternately fed into melting equipment called a cupola. While burning in the cupola to melt the iron source, the coke remains at the bottom of the cupola as “bed coke” and plays the role of adding carbon to the iron source. However, coke emits CO2 not only when it is used but also during the mining and production processes. Furthermore, the production volume of coke is on the decline worldwide, and in order to procure it, we rely on imports from overseas. Given these circumstances, stable procurement in the future is also a cause for concern.
Discarded coconut shells turned into fuel
Aisin Takaoka has turned its attention to plant-based biofuels as an alternative fuel to coke. For biofuels, the CO2 absorbed during the plant growth process offsets the CO2 emitted during the process of melting the iron source, making the net CO2 emissions zero. Moreover, unlike coke, there is no need to worry about running out of raw materials.
After extensive testing, we chose to focus our efforts on coconut shells due to their high oil content. Since Aisin Takaoka’s Indonesian subsidiary has used coconut shell charcoal as a carburizer in the melting process, full-scale development of coconut shell-based fuel began in 2021.
Coconut shells are the shells of the seeds of oil palms, which are common in Southeast Asia. Oil palms grow quickly, and oil palm fruits can be harvested three or four times a year. Palm oil, which is extracted from the fruits, is used as food, and palm kernel oil, which is produced from the seeds, is used in cosmetics and soaps. Indonesia is the world’s largest producer of palm oil. In recent years, the spotlight has been on post-extraction coconut shells because they can be used as biofuel for power generation. However, approximately half of them are still discarded. By effectively using discarded coconut shells, it is possible to reduce the amount of waste generated while also creating environmental protection measures.
Unique manufacturing technology achieves performance equivalent to coke
The newly developed bio-briquette charcoal is made by carbonizing and molding coconut shells. We have confirmed that our bio-briquette charcoal, made using unique manufacturing technology, is strong enough to withstand the cupola, has a high amount of heat, and has no negative impact on the equipment or products.
Mr. Junji Nitano, General Manager of the Production Engineering Division, Aisin Takaoka, who led the development, says, revealing the difficulties of development: “The most important thing is hot reactivity. If the coke’s combustibility is too good, the bed coke layer will be low, and the coke will not be able to provide enough carbon to the molten metal. The challenge for the future is to make its quality uniform so that the bed coke remains at a constant height even during continuous operation.
In a demonstration experiment, after replacing 50% of the coke with bio-briquette charcoal, we operated the melting furnace for six hours and succeeded in producing products with quality comparable to that of mass-produced products. We have completed a demonstration evaluation with a replacement rate of 50% and will set up a demonstration line to begin production in fiscal year 2024. We plan to start mass production in 2025 and replace all fuel that we use with bio-briquette charcoal by 2030.
We are considering selling bio-briquette charcoal to other companies in the same industry in the future. Mr. Nobutaka Uchida, President of Aisin Takaoka, says with enthusiasm: “There are many small- and medium-sized companies in the cast iron industry. We hope to contribute to decarbonizing the entire industry by spreading the use of bio-briquette charcoal, which can help us to address the issue of carbon neutrality and risks in the procurement of coal-based coke while using existing equipment as is.” Since cupola furnaces are used not only in Japan but also in countries and regions around the world, including Europe, which have strict environmental regulations, we are considering expanding this product overseas in the future.
The potential of plants will be key to achieving CN
The AISIN Group works on a variety of initiatives in both production and product areas to achieve CN. In terms of production, our goal is to achieve carbon neutrality in production by 2035 and zero CO2 emission in plants by 2040. To do this, we promote multifaceted technological development that will lead to solving environmental and social issues. Our main objectives lie within three pillars: power source/heat source/waste-free; clean energy; and resource circulation aimed at zero waste.
In terms of the use of clean energy, we have already made steady progress in developing technologies that use solar power generation, methanation, and hydrogen, and the development of bio-briquette charcoal is part of this initiative. There are high hopes that this product will become a “dream fuel” that will bring breakthrough technological innovation to the challenging field of cast iron production.
Plants, which take in CO2 and produce oxygen through photosynthesis, have great potential to become a key to achieving CN. To protect the global environment and our lives, the AISIN Group will use its wisdom and hone its technology to build a society where everyone can live with peace of mind in harmony with nature.
■ Click here for Aisin’s initiatives for carbon neutrality.
Making Carbon Neutrality a Reality