Facing the Challenge of Developing the World's First Valve for Liquid Hydrogen-Powered Vehicles
Jun.17, 2024
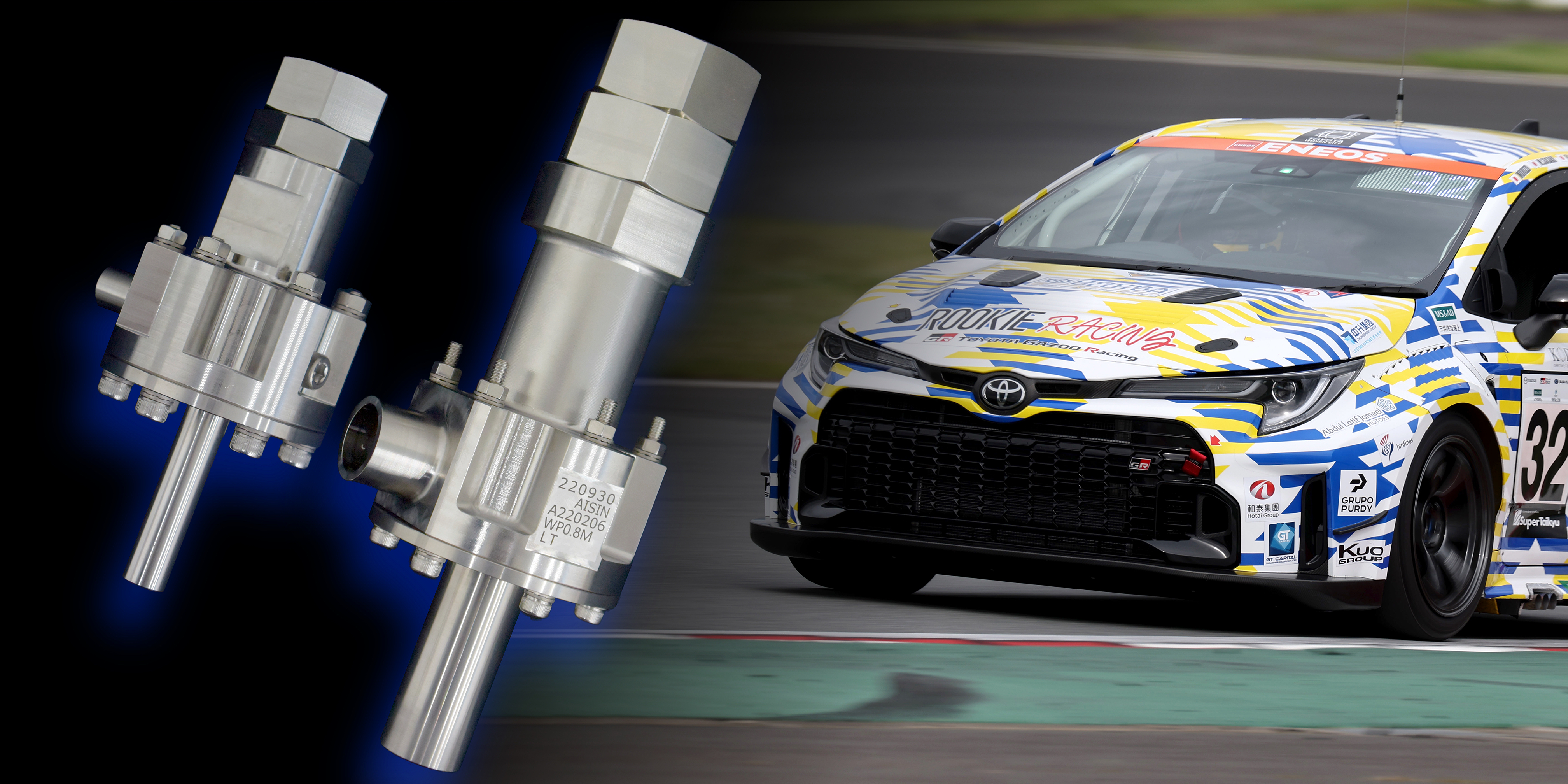
The automotive industry is exploring various options, including electric vehicles, to achieve carbon neutrality. A new option in this trend is the development of hydrogen-powered vehicles. To accelerate this effort, Toyota Motor Corporation competed in a race in 2021 with a vehicle fueled by compressed gaseous hydrogen. In addition, in 2023, Toyota participated in a race with the world’s first liquid hydrogen-fueled machine and successfully completed the race.
This world’s first liquid hydrogen-powered vehicle incorporated AISIN’s cryogenic valve technology. The road to completion was filled with difficulties beyond imagination. The project members spoke about what went on behind the scenes in the development process.
Taking part in a world-first project, leveraging unique technology developed by AISIN
For the development of a liquid hydrogen-powered vehicle, AISIN decided that its own technology could be put to good use, and so it negotiated with Toyota Motor Corporation to manufacture certain parts. These were the two valves AISIN began developing in January 2021: the boil-off gas valve and the first safety valve.
Hydrogen is a substance that becomes liquid at the extremely low temperature of –253°C. In liquid hydrogen-powered vehicles, it is stored in a double-wall, vacuum-insulated fuel tank similar to a Thermos flask. However, various components are installed on the fuel tank, so some areas of the tank cannot be completely vacuumed, through which heat enters, causing natural evaporation. When hydrogen becomes a gas, its volume increases by 800 times. Even a small amount of evaporation can increase the internal pressure of the tank and, in the worst-case scenario, cause the tank to burst. To avoid these problems, there’s a boil-off gas valve, which adjusts the pressure inside the tank to a constant level, and a first safety valve, which instantly releases pressure in the event of a sudden increase in pressure.
Munehiro Tashiro, who leads the development, said that these two valves were created from technology developed by AISIN.
“First, the advanced valve technology that controls hydraulic pressure in automatic transmissions is an area in which AISIN excels,” said Tashiro. “And the technology to make it function properly at the extremely low temperature of –253°C is based on knowledge and experience with freezers that has been acquired over many years. Although the purpose of use may be different, the function is the same, so we thought that if we made good use of AISIN’s unique technology, we could make this valve a reality.”
Furthermore, AISIN’s unique strengths, which some other companies don’t possess, also supported the development.
“The valves made by manufacturers specializing in safety valves are for stationary use. In other words, they are of a type that is attached to equipment that does not move from its location. In this project, we were installing the valve on a racing vehicle, which is a moving body. Being able to respond to this was a strength of AISIN, with its deep knowledge of car manufacturing,” said Tashiro.
Thus began the development project for the world’s first valve for liquid hydrogen-powered vehicles. But along the way, unexpected difficulties awaited.
Struggling in unknown territory to achieve the precision required at the nanometer level
They took off believing that they had the required knowledge. However, development did not go smoothly. The biggest challenge was how to handle the extremely low temperature of –253°C. Kazushige Nakagawa, who was involved in the development, explains the difficulties involved.
“We found that in the realm at –253°C, the sealant inside the valve that prevents gas from leaking shrinks and becomes unusable. In that case, the only way to prevent leakage is to construct a clearance-free on-off valve. This was the challenge,” Nakagawa said.
“No matter how precisely a metal valve is machined, slight irregularities will always remain on its surface. Moreover, hydrogen is the smallest molecule in the universe. Valves with average precision will allow it to pass through. When we asked our in-house Science Analysis Engineering Department to analyze it, we found that the contact surfaces required precision on the nanometer (1/1,000,000 mm) level. This was a realm that no one at AISIN had ever experienced,” Nakagawa added.
“The only way to achieve this is through a special process called ‘lapping.’ Moreover, how many companies are capable of processing with ultra-high precision on the nanometer level? Since the deadline was fast approaching, we contacted every processing company we could find. But we kept getting turned down with the words ‘We can’t do that.’ Among them, there was only one company that was willing to listen to us, and we immediately sent Tashiro to visit them,” Nakagawa recalls, describing the tense situation at the time.
That very same day, Tashiro brought along drawings and prototypes and explained the current situation frankly. Perhaps the company could sense the team’s passion for development because they agreed to undertake the machining. A ray of light shone on the team as they continued to struggle in unknown territory.
The team’s passion for developing world-first technology began spreading to people around them
Meanwhile, when the staff analyzed the safety valves of specialist manufacturers, they found that the valve structures and assembly methods were slightly different. “Although hydraulic control valves and normal safety valves had the same mechanism, they were still different things. Here too, we continued to reach out to safety valve manufacturers, seeking cooperation,” Tashiro recalls.
Eventually, a company that resonated with the team’s enthusiasm came along. Tashiro headed out again with drawings and prototypes. When he was shown into a room and explained the current assembly method, the company’s engineers raised their voices one after another, saying things like, “That won’t do,” “It will make this surface rough,” and “In that case, you should assemble it like this.” The room gradually became filled with the excitement of a development group meeting. They wanted to complete a world-first project using their own parts. The passion of AISIN’s development team had eventually crossed company boundaries and spread to the minds of many engineers.
“We were truly thrilled when we completed a prototype that met all the requirements and passed the safety evaluation test conducted in Canada in September, 2022. Time spent for the development was just nine months from the start. We were on a tight schedule and even one stumble would have meant failure, but I think everyone on the team, and the many people from our partner companies, did a great job.”
Tashiro recalls the stress of those days, which was like walking a tightrope.
Now the question remains as to whether it functioned without any issues in actual races. Time would tell as an actual race was quickly approaching.
Finishing the debut race successfully; and moving quickly to make progress for the next step
The valves, which were completed through the combined efforts of the team, were installed in Toyota’s #32 ORC ROOKIE GR Corolla H2 Concept, which competed in a 24-hour endurance race held at Fuji Speedway. AISIN’s development team also rushed to the venue and watched anxiously to see how the grueling debut race would finish. The result was that the world’s first liquid hydrogen-powered vehicle completed the course successfully. The valves continued to function normally, proving their reliability.
“At the moment the car reached the goal, I felt more relief than emotion. What was even more moving was that all development team members were able to share this moment together,” said Tashiro.
The development project for valves for liquid hydrogen-powered vehicles did not end here. Having had determined the specifications required for the race, the team took on the next step, which was to work on significantly reducing the weight. That was an amazing challenge, aiming for less than half the weight of the first-time valves.
“The first-time valves, as we focused on preventing hydrogen leaks, were a little over-specified. This time, by optimizing rigidity and other factors, we were able to achieve a significant weight reduction,” explains Takayuki Hayashi, who is involved in the development.
“We don’t intend to end the project with racing but are viewing the project from the perspective of mass production. The challenge is how to eliminate unnecessary bulkiness and processes. This weight reduction implies a realistic approach with an eye to such future needs,” said Hayashi.
The goal is social implementation. The team’s unwavering attitude is also evident in their efforts to reduce the weight of the valves.
The rule that most fortified the team of novices that achieved a world’s first: no team member is blamed for failure
Every time this project faced difficulties, it was the members’ passion and initiative that overcame them. Tashiro says that the roots of this success lie in an organizational management style that is unique to this team.
“When I was put in charge of this team, I decided to blame no one. When something went wrong, I encouraged the members to ask themselves, ‘Why has this happened,’ identifying the problem on the spot and discussing it together, instead of putting someone on the spot by asking, ‘Why?’ The point is never to blame anyone. Instead, I tried to take it in a positive way, thinking, ‘Now that I understand that that was no good, I can move on to the next step.’”
If you are not punished for failure, you will no longer be afraid of failure. When you are no longer afraid of failure, you become more proactive. When the team found the lapping service company, it was also due to the members’ spontaneous actions that led to the discovery. “I think everyone has their own abilities. It is the job of those in charge to ensure that they use their abilities well. This team isn’t elite either. It’s actually a collection of novices,” Tashiro said, and both Hayashi and Nakagawa nodded with laughs.
There is an open atmosphere where you can say whatever you want. They joke around and have a fun conversation, but they get to the heart of the matter. That is how they brought this world-first project to fruition. These members have a strong passion that rivals that of the elite, believing in each other’s strengths, acting without being told to do so, and pushing the team forward. Perhaps a project that will astound the world again will be born from here.